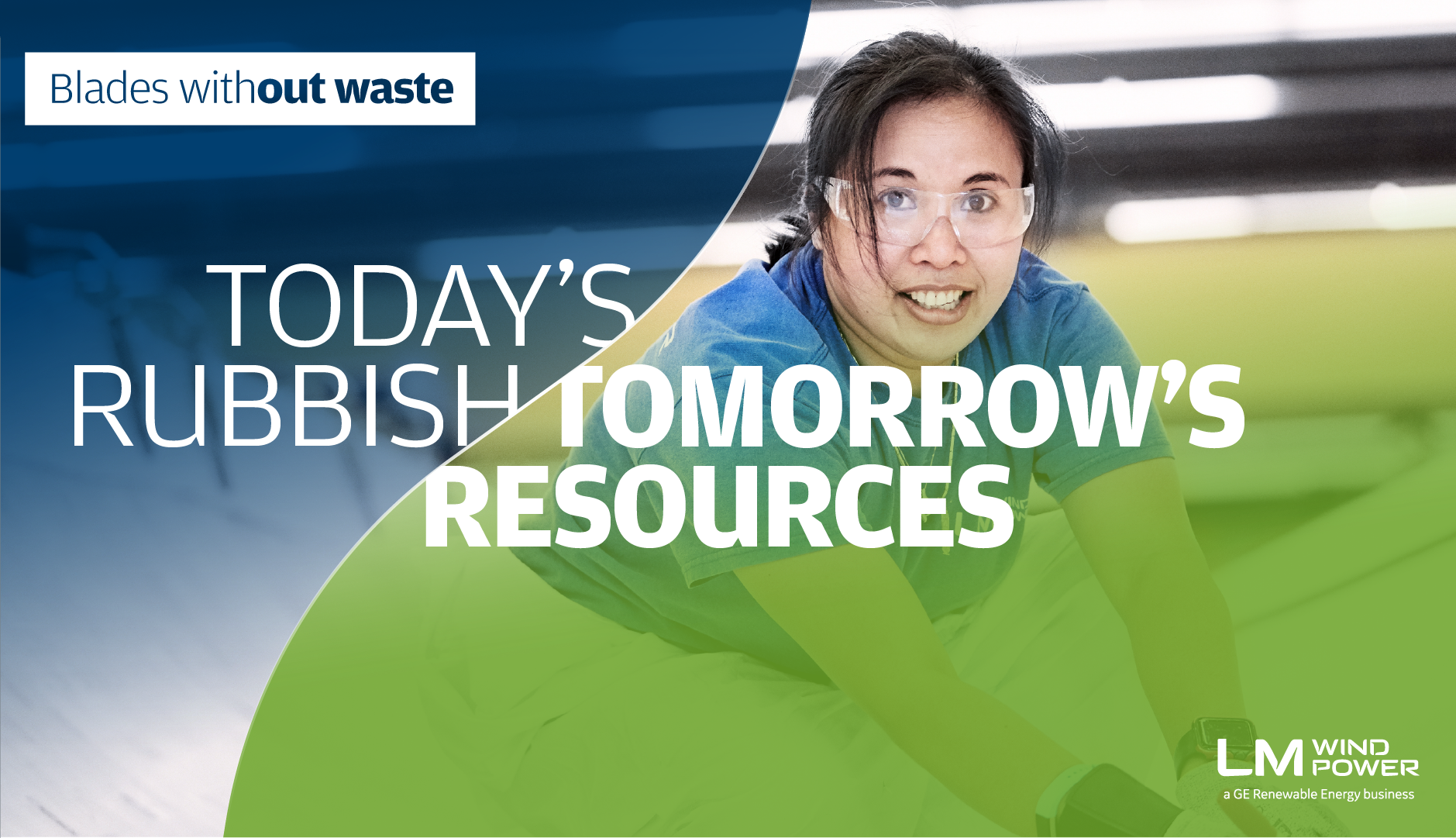
Scaling up Circularity: Advancing sustainable solutions to unlock the value in waste
The adage "reuse the past, recycle the present, save the future" is well known to many of us. It motivates us to be more environmentally conscious, to practise behaviours and take actions that will lessen our overall carbon footprint and help address issues related to climate change.
As blade builders we know that for the wind industry, generating manufacturing waste is inevitable. Nearly 20% of the materials purchased for blade manufacturing do not end up in the finished product. Additionally, according to research, the volume of waste from blade manufacturing is predicted to exceed that of end-of-life blades in the ensuing decades.
To tackle these challenges, we are designing out the waste from our blades. Through our commitment to make Zero Waste Blades by 2030 we are exploring new ways to reduce, recycle and reuse manufacturing waste and developing a circular economy for all excess materials from manufacturing. This means that by 2030, we will not send any materials or packaging to landfill or incineration without energy recovery.
Protecting resources
In line with the above pledge, over 40% of our waste was recycled in 2021, compared to 27% in the year before. Simple steps like segregating waste into color-coded waste bins kept in the production area (for collecting glass fiber, cartons and other industrial waste) went a long way in making it easier for teams to send this assembled waste to recycling partners.
“Waste segregation is a challenging process. If you do not segregate correctly then the amount of waste that should have been sent for recycling reduces, which is not desired- from a resource reuse perspective and has higher cost implications,” says Julio Sobel, Manager, Health Safety & Environment at LM Wind Power's blade facility in Suape, Brazil .
To educate employees at the plant, in 2020 LM Wind Power Suape launched the “Waste Killer” initiative, through which local teams, including new employees, are trained on multiple aspects related to waste - the different types of waste generated during manufacturing, disposal standards for each of them, inspection of collection and disposal processes. Sobel’s team works closely with the “waste killers” and production teams and conducts regular training and exercises to drive collective actions for proper waste management practices.
We also aimed at reducing direct consumption of materials like carbon, glass, resin and glue, which are used in the blade making process. These materials either become a part of the final product or are discarded as manufacturing waste. To lower our consumption of carbon, we reviewed the spar cap building process. Spar caps make up the support beam, which runs the length of the blade and are built from carbon planks that come in various lengths. These carbon planks are extracted from carbon coils available in three standard lengths. By optimizing the carbon coil cutting sequence, length of the coils and the process set up, we lowered our carbon consumption and scrap percentage from 10% to 1% in 2022, leading to cost savings.
In another successful initiative to reduce glass fiber waste, we were able to close 40% of the gap from the design stage to the actual raw material consumption, by organizing multiple Kaizen events across our plants globally, to first identify key areas followed by targeted process improvements, and further engaging with suppliers to reduce overconsumption. Specific projects like web 2D cut to shape glass, glass roll length and width optimization developed over the past year, enabled us to lower the waste and protect our resources.
Sustainable alternatives for conventional waste disposal methods
Traditionally non-recyclable waste such as Fiber Reinforced Plastic (FRP) waste, resin & glue, spent solvents etc. are disposed of through incineration. While the process generates heat that can be used for heating homes and can even generate power through steam turbines, incineration does not necessarily promote recycling and reduction in waste.
To find sustainable alternatives to incineration, our teams in India collaborated with a local university (Bangalore University), to study how FRP waste can work as an additive in concrete cement used in the construction industry. Their analysis showed that by adding FRP waste, the mechanical properties of concrete cement enhanced by over 10%. After receiving regulatory approvals, FRP waste is now being reused for construction purposes. Inside our Dabaspet plant, a 3000 m long road is constructed using FRP waste as seen in the picture below.
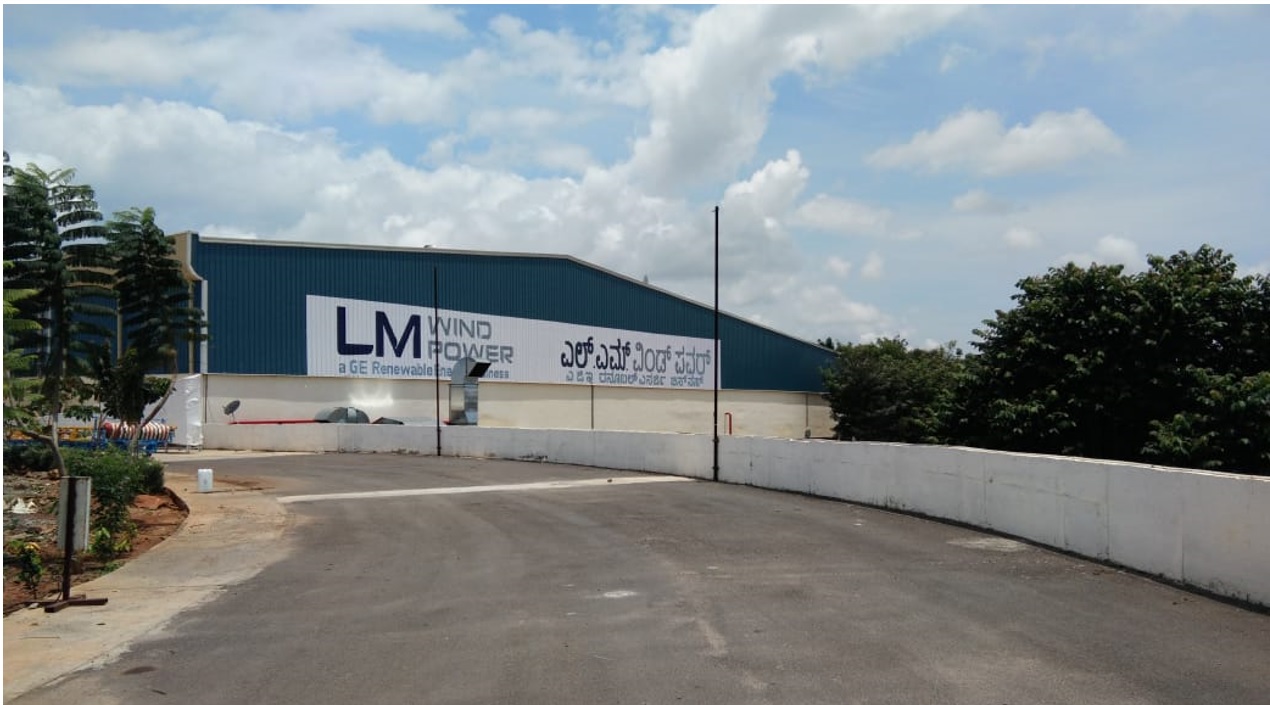
Additionally, resin and glue waste are now being used as an alternative fuel in the tile manufacturing industry. When mixed with coal and fed into a reactor, the combined mixture converts into ash that is used in making tiles.
Overcoming challenges and together solving for circularity
The stumbling blocks associated with waste disposal, recycling, and reuse are numerous. Right from the location of the manufacturing plant to absence of competition in the market, to failure in recognizing the opportunities that waste provides us with - there are many factors that influence decisions.
Corey Kaltenberg, from the EHS team in Grand Forks (US) explains: “In our region, we have a very limited number of vendors who are readily available to recycle different products. This immediate lack of competition affects pricing, volume and other aspects associated with sustainable waste management practices.”
Changing perceptions and understanding basic facts about waste management is equally necessary.
Although there are many obstacles to efficiently reducing manufacturing waste, we consider this as an opportunity to find innovative and sustainable solutions, to ultimately unlock the true value of wind, and capture the green electricity that it helps generate. With our technology leadership and strong global partnerships with suppliers and customers we will be able to design out the waste, include more recyclable materials in our processes and effectively engage in a circular economy, enabling our customers to further deliver clean energy worldwide.