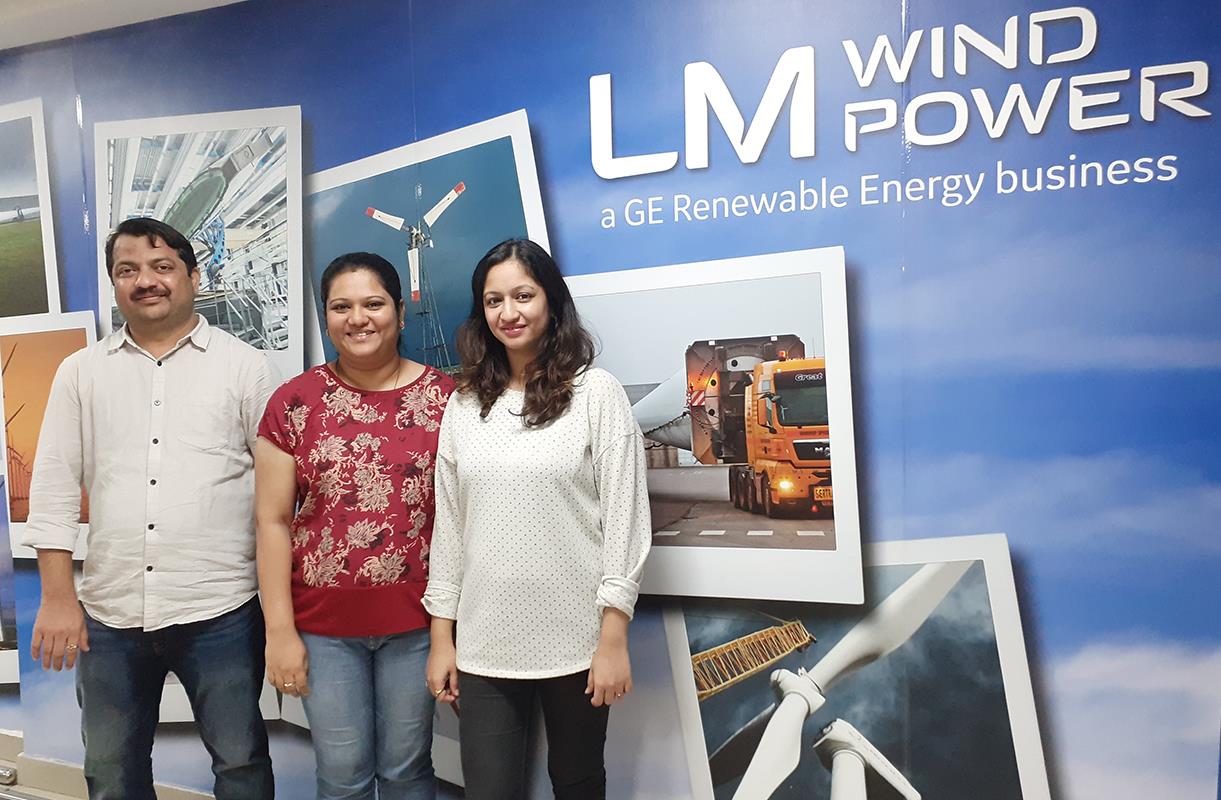
Technology Center India: Living the One Team philosophy
Founded in 2007 with just 15 engineers, technology center India (TCI) is today a vital hub in the LM Wind Power global network with over 200 employees working across all aspects of the business including new product introduction (NPI), supply optimization and making sure our plants run as efficiently as possible.
We spoke to three of the TCI team – Prajna - Lead Engineer, Material Engineering; Rahul Bangar - Manager, Transportation Engineering, and Shantanova Bora - Senior Analyst, Global Operations Quality – about why they enjoy working at LM Wind Power, and how they see the role of TCI evolving as part of the One Team approach.
What attracted you to work for LM Wind Power?
Prajna: I joined LM Wind Power back in February 2011, from the automobile industry where I was a Quality Control Engineer working in a high volume, fast cycle production environment. As a metallurgist by profession, I was always very keen to move away from production into R&D and the role at LM Wind Power meant that I could do just that. I was also personally motived by the fact I was going to help deliver renewable energy which gives me a sense of pride, which just wasn’t there with automobiles.
Rahul: I started my journey with LM Wind Power in January 2011 following a recommendation from a colleague I knew who worked here. I come from an aerospace background and was working with electromechanical & hydro mechanical systems, where everything was tiny and measured in microns and millimeters. I was attracted by renewables as an industry and suddenly my world of transport equipment engineering involved huge components with greater tolerances, so it was a really exciting change and challenge for me in the beginning.
Shantanova: I joined LM Wind Power as part of the service team in 2010, running Service reports, doing invoicing and other tasks which helped the service technicians carry out repairs to the blades on site. LM Wind Power was not really that well known at the time, with little media presence - unlike now. I was working for Hewlett Packard which was very well known, so it was a big decision to join LM Wind Power, but it was based on my interest in the role. After four years I made the switch from Service and joined the Global Quality team. LM Wind Power has a good flexible working policy and allows me to manage my working life and my childcare responsibilities.
Which team do you work in and what achievements are you most proud of?
Prajna: I’m working as part of the Material Engineering team and every day there is a new challenge which I love! When the team was first set up, it was all about getting us trained and enabling us to come up with all the material and qualification specifications that were needed – it really was a very supportive environment. Now we are in a new phase of our development and being exposed to techno-commercial aspects of the business, working in partnership with Sourcing to ensure that whatever we are designing from an engineering perspective is also commercially feasible in the market. I also love the challenge of working with the suppliers to take cost out of the product without compromising on quality. I am the only metallurgist at TCI and in the country, so everyone knows me as the metal specialist which gives me a great feeling of pride and confidence.
Rahul: I am Transport Equipment Engineering manager and proud to say that from a one-person team, we are now six people and growing. Increasing blade size, changing regulations, and growth in demand for transport rigs are the drivers for this expansion. We deal with road and sea transport, and support everything that’s needed to move the blades from the factory to their ultimate destination, which can be extremely challenging at times but there’s always new things to learn!
Shantanova: As a member of the Global Quality team, I’m responsible for reporting the Key Performance Indicators and Process Indicators which show us a plant’s performance on quality. The plants provide us with about eight different metrics in a variety of ways. We consolidate that data into a central system and generate a quality score for each plant. I also took over a dashboard project recently in the Tableau Platform, which helps each plant to see how they’re performing on quality, but also compared to all other plants. I’m very proud that I managed to learn the software and complete the project in three months alongside a couple of my colleagues.
What role does TCI have as part of the LM Wind Power family?
Prajna: I feel like TCI is at the heart of everything, giving guidance to the plants and solving issues that arise from production. Equally, when the blade goes to the customer, if they have any issues with quality or they need further information, it comes back to TCI to resolve. So, we are helping our plants make high quality blades and making sure our customers get the best performance possible out of our products.
Rahul: I feel that everyone in LM Wind Power, regardless of their location, takes ownership of their own deliverables and helps the entire company move forward. And TCI is no different.
Shantanova: When I first joined TCI it really felt like a support function and I have seen us evolve into a hub that drives projects and makes decisions, rather than just responding to requests. I don’t think we’re completely there yet, but we are definitely making progress. We’re also doing more to emphasize the importance of accurate data and to help improve it as it can strongly influence any changes the plants have to undertake to improve their performance.
Describe what you see are the biggest opportunities and challenges for TCI.
Prajna: When I joined LM, our blades were 12m+ and now we are making blades 77.4m+ in India and 107m in France. There is a huge appetite for bigger blades which represents an exciting opportunity for us. The challenge is that as the blades increase in size, the designs become more complex, which is great for enhancing our skills but also means we need more subject matter experts for innovation and energy optimization. For example, there is now a dedicated transport team that work on ensuring the optimal transportation of these huge blades.
Rahul: When I first joined TCI, transport was not regarded as an important function. But now everyone understands the importance of transport as it represents such a significant chunk of the product cost. Every blade type has dual sourced frames qualified so we are actively managing dozens of different variants of transport frames, as well as developing new ones which is challenging. We never compromise on cost when it comes to the safety of everyone involved in getting the blades onto the transport rigs and delivered safely to the customer. As we’re developing new blades and technologies, there are a huge amount of opportunities for LM Wind Power. And each function has to continually find ways to do things better to capitalize on those opportunities.
Shantanova: The collaboration between TCI and the plants is the biggest opportunity that we have to create the best blade at the right cost and quality. TCI’s contribution should help support and improve the plant’s performance. We do work well together but I feel we can be even more closely aligned so that plants have no hesitation in contacting us and asking for our help.
How do you take advantage of the global infrastructure of LM Wind Power and GE?
Prajna: Working with colleagues in other countries is invaluable for sharing knowledge and experiences. I have also had the opportunity to travel to Denmark, and China several times to do process audits with our suppliers as well as the Netherlands where our financial group is based. From an IT perspective, the move to Skype from IP phones has been transformational – you can get hold of anyone now at any time. Additionally, through the global Cypress 2-piece blade program, I have begun to work with colleagues outside of LM Wind Power, in GE Renewable Energy who have heard about my reputation as the metals expert and want to seek my advice. Through GE, I have also been involved in the Women’s Network here, which has raised important topics such as breast cancer awareness and sexual harassment in the workplace.
Rahul: Our team supports the technical transport engineering requirements for all the manufacturing plants and all the NPI activity that happens across the global LM Wind Power network. Sometimes that means travelling to some of the plants as well as visiting customers. We have colleagues based in Kolding, Denmark who lead the project management aspects and we deliver the engineering expertise. Our success is down to the fact that we really feel like we’re one team working together.
Shantanova: I talk frequently to Plant Supervisors and Quality Managers across the global organization and of course also work with my colleagues in the wider Global Quality team, so I really feel like a member of one big LM Wind Power family!
Learn more about LM Wind Power’s global network of Technology Centers.
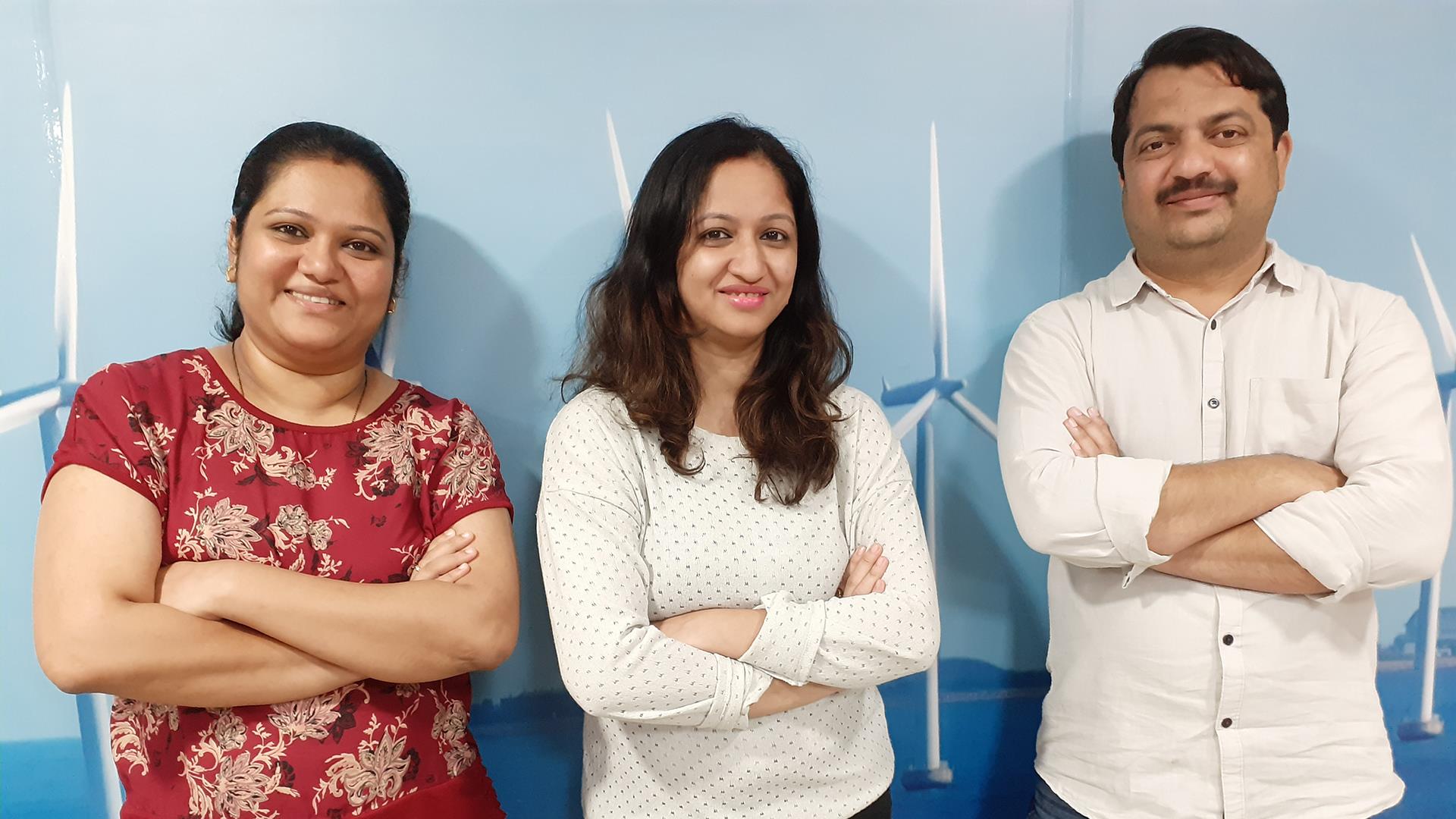
TECHNOLOGY CENTER INDIA
Meet the team
From left to right: Prajna, Lead Engineer, Material Engineering; Shantanova Bora, Senior Analyst, Global Operations Quality; and Rahul Bangar, Manager, Transportation Engineering.