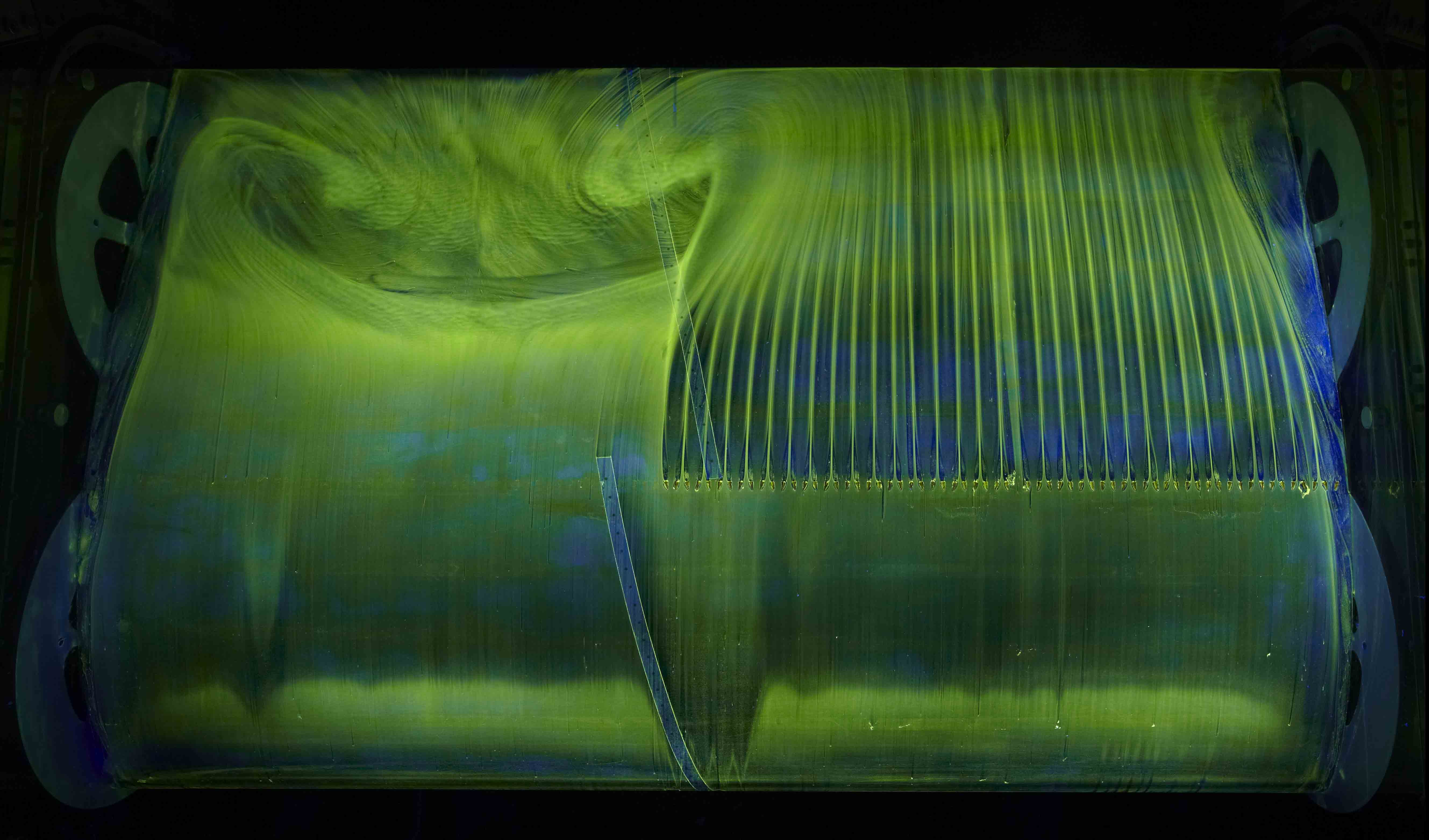
Enhancing Reliability: LM Wind Power’s Wind Tunnel Validates Blades for Turbines of the Future
LM Wind Power has over 40 years of deep domain expertise in the development of wind turbine blades, spanning from over 10 meters to colossal structures that extend beyond 100 meters. Aerodynamics plays an important role not only in the reliability of the blades but also maximizes the energy extracted from the wind during each a rotation. To ensure this, our blades undergo various tests at our onsite research facilities, which includes a rain erosion laboratory, full-scale test centre and a wind tunnel.
World’s First Wind Tunnel for Blade Tests:
Longer blades capture more energy but has its own set of design and performance challenges. When the length of the blade crosses 100 meters, the pressure built up on a rotating blade is huge – equivalent to ten mid-sized trucks! In strong winds, the blade can flex by as much as 8 meters in each direction and therefore, resulting vibrations in the rotor need to be carefully managed.
This is where our aerodynamic experts come into the picture. “High ambitions to improve the aerodynamics of wind turbine blades through extensive wind tunnel testing motivated LM Wind Power to build a new Low-Speed Wind Tunnel (LSWT) from scratch, meeting up to date requirements to testing conditions and test section flow quality,” says Jesper Madsen, consulting engineer for aerodynamics.
The facility, situated at our Test and Validation Centre in Lunderskov, Denmark, was inaugurated in 2006 and is the world’s first wind tunnel that is custom designed for research and testing of the aerodynamic properties of rotor blades. The tunnel, 7.00 m length, 1.35 m in width and 2.70 m in height, can generate a maximum wind speed of 380 kms/hr or 105 m/s. A cooling system built within the tunnel removes the excess heat at high wind speeds.
Optimizing performance and design:
At the wind tunnel, our experts can exactly define how the blade will react in different conditions. Leveraging this data, LM Wind Power’s specialist team carefully adjusts the blade profile to minimize torsion, flex and vibrations – enabling them to develop longer blades that drive safety, efficiency and higher energy yields for the customer.
We test airfoil shapes, add-on devices such as vortex generators, flaps, serrations, etc. and also study sensitivity to understand the impact of geometry deviations, surface roughness, and leading-edge contamination or erosion.
For airfoil testing, the test setup includes a high accuracy turn table device for holding the airfoil model and an automatic traverse system holding a wake rake. Nearly 300 sensors are used to characterize the airfoil flow including differential pressure sensors and a load cell system. An automatic data acquisition system allows a high level of uniformity between different tests. To qualify flow patterns with flow visualization techniques, we apply established methods utilizing infrared camera, tufts, smoke and oil.
The wind tunnel is also used to investigate the impact and performance of various add-on devices like vortex generators, flaps, and serrations. Design and optimization of add-on devices involves several additional variables and parameters like geometric details, size, location, and spacing, which impact performance. Numerical predictions will often become very expensive or inaccurate resolving geometric details and flow complexity, so wind tunnel experiments are often the only option.
Besides knowing the performance of the optimum airfoil shape and add-on device configuration, the sensitivity to various real-life conditions can be very critical. These include geometry deviations, surface roughness, and leading-edge contamination or erosion. Some impacts are very difficult to predict, especially if there are combined effects, so wind tunnel testing can be the only option.
Testing for Reliability:
An increased need for experimental verification has appeared as a follow of the trend to tailor airfoils for operation on specific wind turbine blades as opposed to previously where airfoils were selected among a limited variety of existing families. The continuous optimization of new blades occurs to increase efficiency as well as to move the barrier for how long blades can be for both existing and new turbine platforms.
The tailoring of airfoils and add-on devices opens up for further design optimization, but also moves us away from our knowledge base. Although speed and accuracy of simulation tools are continuously improving, numerical predictions have not yet reached a level where the accuracy is sufficient to eliminate the need for experimental verification.
“We are the only wind turbine blade manufacturer to have our very own wind tunnel and in-house testing facilities for full scale blade tests. This gives us the highest level of flexibility, to perform blade tests every day – a significant advantage over others and helps us deliver the blades to our customers sooner,” says Carlo-Enrico Carcangiu, director of the aerodynamics team.
He explains: “To test the reliability of wind turbine blades, we examine aerodynamic properties and experiment with different solutions for actively controlling the loads on our blades. With advanced numerical simulations, we generate aeromechanical designs which are validated in our wind tunnel.”
Knowledge Centre for the wind industry:
LM’s wind tunnel is seeing increased use by our customers for testing their in-house designed propriety airfoils. The speed of execution, quality of measurement, competitive cost, technical know-how along with experienced engineers and technicians are adding value to our customers.
What’s Coming Next?
One of the upcoming challenges at our wind tunnel is to conduct high precision experiments to measure the sound level generated by an airfoil. This means new skills, measurement technologies and a turning of the current wind tunnel to a low sound level aero-acoustic laboratory.
Further, the wind tunnel is expected to go through a major upgrade soon. The measurement system, including, sensors along with the data acquisition system will be upgraded. A new set of cameras, conventional and infrared, will be installed for better visualization of flow features.
Consistency is the key:
The many years of experience operating the LM Wind Power wind tunnel has shown the importance of consistency, i.e., being able to repeat tests and conditions as well as having good benchmark data. Consistency comes from standardized and automated testing and post processing, but also from skilled and experienced wind tunnel technicians performing manual work.